PSR-1600-W
Reciprocating gantry type precision sanding, grinding, and polishing machine
Our PSR-1600-W is equipped with single wide abrasive belt head, wet operation. It is gantry structured, meaning the working table is able to carry the work piece to move back and forth reciprocally under the wide abrasive belt head to process multiple passes on the work piece to achieve the optimal desired surface requirement such as specific surface roughness. There are several different ways to “clamp” the work piece, most commonly: vacuum suction table or electro-magnetic table. For achieving specific roughness on a work piece, a specific combination of wide abrasive belt is required, usually goes from coarse to fine grit. To avoid exchanging abrasive belt frequently, up to 4 wide abrasive belt heads is configurable. A fine surface roughness of Ra 0.4 μm can be achieved.
Machine characteristic overview:
-
Wet operation
-
Reciprocating process, work piece will be processed multiple passes. No need to feed in work piece repeatedly.
-
Wet operation to prolong abrasive life span, and cool down the parts during the process to minimize parts deformation. Water soluble cutting fluid is used.
-
Wet operation to greatly reduce metal particle dispersing into air
-
Automatic cutting fluid filtration unit
-
width from 1000 till 2500 mm possible
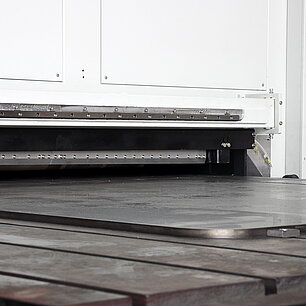
PSR-CALIBRATE series
The PSR-Calibrate series sheet calibration machines can handle titanium, stainless steel, aluminium and other metal sheets up to 10.000 mm long and 2,500 mm wide. By grinding the upper and lower surfaces three or more times in a row, and with the sheet upside-down during the second time, a thickness accuracy tolerance of 25 μm is attainable, making this calibration process real precision technology. The main application area of such calibrated sheets is the aircraft industry.
Belt grinding versus stone grinding
The PSR-CALIBRATE series sheet calibration machines, may be regarded as a successful spin-off of our deburring expertise with grinding belts Mixed with our surface grinding knowledge and experience. In the precision engineering world, stone grinding is mostly preferred to belt grinding because stone grinding has the ability to machine 3D-curved surfaces. this start to be seen in metal grinding too. On the other hand, belt grinding is limited to the machining of flat surfaces, although cylindrical forms can be handled too.
Good Abrasive belts producers claim some important advantages for the application of their belts: long lifetime, high cutting rates and dry as well as wet application. A surprising property is the regular arrangement of abrasive grains – aluminium oxide, zirconium oxide, silicon carbide or special ceramic – on the base material. Because of the identical orientation of each abrasive grain, the grinding particles nearly always show the same cutting and clearance angles. This is contrary to the stochastic orientation of grains in stone grinding discs. And changing a grinding belt requires much less time than changing and adjusting a stone grinding disc.
A typical PSR-CALIBRATE Series process combines a fast rough grinding cycle followed by up to three spark-out passes, with the sheet, which is positioned on the powerful vacuum table, then rotated and the cycle repeated on the opposite face. The result is a thickness accuracy across the entire sheet of 0.25 μm with the major benefit of the process creating a ‘short-scratch’ finish, which means there is no direct path from inside to outside, making it ideal for use in applications such as sumps, cylinder heads, etc; the surface finish is such that potentially, gaskets can be eliminated. This is possible due to the combination of machine and belt technology, with new abrasives offering long life, high cutting rates thanks to the creation of a regular arrangement of abrasive grains, whether they be aluminium oxide, zirconium oxide, silicon carbide or ceramic. The result being greater consistency over surface finish when processing a range of materials. Wide belt grinding also has advantages over milling, as thinner sheets can be processed, and the surface quality is far superior.
Further advantages of using the wide belt approach to high metal removal are its lack of influence on the material being processed and the environment. Using abrasive belts puts less heat into the material therefore eliminating any chance of metallurgical damage or imparting stress into the part.
The reduced cutting forces also require less energy thereby generating savings in power consumption.
Reduce drastic your Grinding costs!
Grinding using stones or abrasive wheels may deliver the surface finish and accuracy, but at the expense of cycle time. Profimach’s alternative, the PSR Series, is a wide belt grinder that can process materials in thicknesses ranging from 0.15 mm up to 100 mm (higher on demand); with stock removal rates of up to 0.2 mm/pass achievable. The result is a significant time saving compared with conventional grinding where cycle times can be halved when removing Titanium material and on other parts where the PSR Series has reduced a conventional 45 minutes grinding cycle down to 2,5 minutes!
Further advantages of using the wide belt approach to high metal removal are its lack of influence on the material being processed and the environment. Using abrasive belts puts less heat into the material therefore eliminating any chance of metallurgical damage or imparting stress into the part. The reduced cutting forces also require less energy thereby generating savings in power consumption. Compares with a conventional grinding machine of "exotic materials", an 80 per cent reduction of energy consumption can sometimes be achieved. These energy savings are increased further when grinding ‘less exotic’ materials such as steel, stainless steel and cast iron, with the latter showing a saving of over 88 per cent.