Reduce drastic your 3D Additive Manufacturing costs!
As the world of manufacturing changes new opportunities arise; one such opportunity for the PSR Series is the grinding of baseplates used in 3D metal printing. Printed metal objects are often created from difficult to machine materials and removing them from the baseplate leaves behind a residue that cannot be easily removed, therefore the plate is written off or need to undergo an expensive and time consuming milling and/or grinding process. Grinding away that residue to bring the baseplate back to ‘as new’ condition using the PSR Series significantly reduces manufacturing costs where 3D metal printing is concerned.
Grinding using stones or abrasive wheels may deliver the surface finish and accuracy, but at the expense of cycle time. Profimach’s alternative, the PSR Series, is a wide belt grinder that can process materials in thicknesses ranging from 0.15 mm up to 100 mm (higher on demand); with stock removal rates of up to 0.2 mm/pass achievable. The result is a significant time saving compared with conventional grinding where cycle times can be halved when removing Titanium printed rests and on other parts where the PSR Series has reduced a conventional 45 minutes grinding cycle down to 2,5 minutes!
Further advantages of using the wide belt approach to high metal removal are its lack of influence on the material being processed and the environment. Using abrasive belts puts less heat into the material therefore eliminating any chance of metallurgical damage or imparting stress into the part. The reduced cutting forces also require less energy thereby generating savings in power consumption. Compares with a conventional grinding machine of "exotic materials", an 80 per cent reduction of energy consumption can sometimes be achieved. These energy savings are increased further when grinding ‘less exotic’ materials such as steel, stainless steel and cast iron, with the latter showing a saving of over 88 per cent.
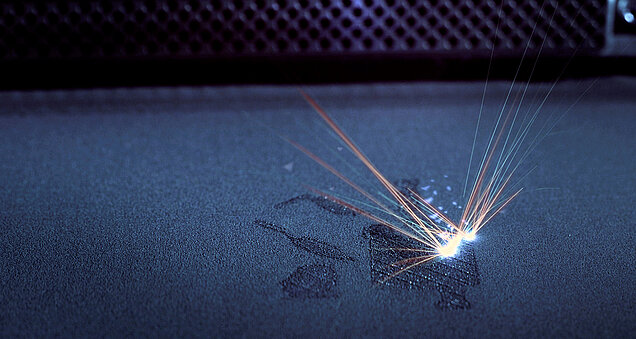