The Right Finish
Automated deburring machines come in many configurations. Make sure you get the right system for your needs
Deburring vs Finishing
Although deburring and finishing involve similar processes, there are important distinctions between them.
Put simply, finishing and deburring machines are designed to remove imperfections that remain attached to workpieces after they’ve been modified by another machine. These undesirable raised edges are commonly known as burrs.
Deburring deals with the removal of the unwanted raised edges caused by previous operations.
Burrs fall into one of two categories:
-
mechanical burrs, which can result from shearing, stamping or folding; and
-
thermal burrs, also known as slag or dross, which can be caused by welding and laser or plasma cutters.
Finishing refers to the broader category of modifying the surface of a workpiece to remove scaling, pitting, enhance its quality or prepare it for next step like coating or painting.
Finishing machines are also used for calibration and stock removal to achieve higher material removal rates and decrease variations, as well as edge rounding.
Other common operations done with finishing machines can include calibration and stock removal (a machining operation done to achieve higher material removal rates and decrease variations), slag grinding (targeting slag produced by thermal cutting machines), and edge rounding (any action that breaks the edge of a metal part, but especially those that form an edge radius).
What do you want to deburr?
Profimach® PRO Steel® Line offers you always an AFFORDABLE and GOOD solution
SLAGGRINDING - DESLAGGING HEAVY THERMAL BURRS
During plasma or gas cutting, strong melting often occurs, with the molten metal sagging on the beam-exit side. In the plasma and flame cutting, the edge of the workpiece will produce slag and flash, and this can be quickly cleaned with very abrasive material or with even heavy slag removal hammers. This so-called slag occurs both on the inner and outer contours of the workpiece and must be removed for economical further processing.
The best, easiest and most economical method is knocking it off using a slag hammer brush made up of multiple flexibly mounted pins. Slag can also be removed by grinding with a soft contact roller and an agressive abbrasive belt.
First choice : H-unit or C-unit with hammer-pin chain links
Second choice : R-unit or T-unit with heavy abbrasive belt
1st: PSCC-Series
1st: PSHTC- Wipe plus Series
2nd: PSGR- Versatile Plus Series
2nd: PSRD-Series
CASTING FLASH REMOVAL
During casting, melted metal often escape from the mould, with the molten metal sagging on the closure and exit side. This so-called flash occurs on the inner and outer contours of the workpiece and must be removed for economical further processing.
When the workpiece allow it in form and size, the best, easiest and most economical method is knocking it off using a slag hammer brush made up of multiple flexibly mounted pins. Slag can also be removed easily by grinding with a soft contact roller and an agressive abbrasive belt.
Castings require all kinds of work prior to their next process, cleaning of flash, preparation of a reference face, dressing of weld seams, or just burr removal we have the machinery.
First choice : H-unit or C-unit with hammer-pin chain links
Second choice : R-unit or T-unit with heavy abbrasive belt
LASER OXIDE EDGE REMOVAL
DEBURRING & EDGE RADIUSSING – FLAT MATERIAL
Why deburr and edge rounding? Apart from the advantages of not cutting your staff and customers, and making the parts fit as the designer intended, a rounded edge ensures even paint coverage thus preventing breakdown of the paint coating on the corners. We have machinery to just break the edge right through to a quantifiable chamfer or radius in excess of 2mm if that’s what’s required
DEBURRING & EDGE RADIUSSING – CLAD MATERIAL
Metal often comes with a protective coating: plastic, galvanising, Zintec and in the aerospace industry, aluclad. Having gone to the cost of buying material with the coating, the deburring and radiussing wouldn’t be much use if it stripped it off. Some of our machines don’t! And they still deburr and radius evenly and controllably.
DEBURRING UPSTANDS & PRISMATIC PARTS
With our advanced and controllable technology we can even tackle up-forms, prismatic parts, louvres and pushouts without damaging surrounding areas. All evenly deburred and radiussed to your specifications.
First Choise : G-unit
Second choice : D-unit and C-unit
WELD DRESSING
Fabrications are put together often with nicely finished stainless steel. They get scratched and disfigured with weld spatter as a result to say nothing of the mismatched grain direction, heat affected zone staining and lumpiness of the welds themselves. We have the solutions to clean up surfaces, match the grain you have, orientate the grain in the direction you want and blend the weld seamlessly into the surrounding surfaces. Manually or automatically.
First choice: T-unit
DEBURRING MACHINED & SHAPED PARTS
What do you want to Finish?
Profimach® PRO Steel® Line offers you always an AFFORDABLE and GOOD solution
POLISHING
Polishing is simply abrading a surface with finer and finer grits until the finish takes on a highly reflective appearance. The grits are applied with ever softer mops which can work on large, wide areas simultaneously, controlled specific areas, or the whole component can be buried in the mop, so called “mushing”. The ultimate ‘Super 8’ finish is a highly specialised version of the commercial finishes usually found in the Europe, involving discs and underwater operation
LASER OXIDE REMOVAL
STRAIGHT-LINE FINISH
ORBITAL FINISH
GRAINING FLAT WORK
Flat parts or surfaces that can be presented flat. The old true-ism is that just one scratch rejects a part, but several million make it look good. We have machines for generating straight scratches, swept finishes, random swirls or our own unique non-directional rain. These can be rough or smooth, generated by abrasive belt, abrasive brush or nylon web material. And they can be short or long, continuous if required.
GRAINING SHAPED WORK
Nearly everything we can do flat, we can do on a shaped component.
Where straight graining is required, blending in with neighbouring faces can require directionally programmable machinery, or the finish can be made random for subsequent hand finishing. Finishes can be rough or smooth, generated by abrasive belt, abrasive brush or nylon web material. And they can be short, long or continuous as required.
CALIBRATING & TOLERANCE GRINDING
With the correct abrasive mineral, travelling at the correct speed, with the correct pressure, and there is enough power to do the job, on a robust enough machine with a sophisticated control system to monitor and maintain the process, high stock removal rates of hard material, to extraordinarily tight tolerances (0.05mm over slabs of 2500x15000mm) can be achieved and maintained. Sanding paper has come a long way, and only few people realise just how far. It's time for you to look into it and get huge savings!
STOCK REMOVAL AND TOLERANCE GRINDING
BRUSHING
Profimach® PRO Steel® Line
offers machines for Reliable and affordable deburring, deslagging, surface finishing, oxide and rust removal, precision calibrated grinding and edge rounding.
DESLAGGING - SLAGGRINDING
During plasma or gas cutting, strong melting often occurs, with the molten metal sagging on the beam-exit side. In the plasma and flame cutting, the edge of the workpiece will produce slag and flash, and this can be quickly cleaned with very abrasive material or with even heavy slag removal hammers. This so-called slag occurs both on the inner and outer contours of the workpiece and must be removed for economical further processing.
Common manual methods for deslagging include chipping it away using a hammer and chisel, or grinding using an angle grinder. In terms of mechanical processes, excess accumulations of material can be removed by grinding with a soft contact roller. Another industrial method is knocking it off using a slag hammer brush made up of multiple flexibly mounted pins.
PRE-GRINDING & DEBURRING
The burr can vary when punching, stamping, fine blanking or laser cutting your materials. Burrs created via laser cutting, fine blanking, stamping and punching adhere to the material in various strengths. Burr formation on laser-, plasma- and gas-cut, or stamped, sheet metal parts often cannot be avoided. Therefore finding a comprehensive deburring solution is crucial. The burr respectively primary burr is a material formation on the cut edge of workpieces that protrudes beyond the original workpiece edges and surfaces.
Other deviations from the target state include, e.g., spatters on the workpiece surface caused by laser cutting, unevenness, or scaling of the surface. A by-product of removing primary burr is the so-called secondary burr. This spreads out in the direction of the workpiece surface and forms due to insufficient removal and simultaneous recasting of the residue material.
Primary burrs, spatters, unevenness and/or scale layers are normally removed by grinding. When removing primary burrs, the focus is on minimising the formation of a secondary burr. In order to remove these undesired secondary attributes from the sheet without leaving a residue, special support units are required for grinding belts, -discs or -sheets.
Deburring refers to the process of smoothing the rough edges of a metal object or component. To some, a part is considered deburred when its vertical burr is removed. To others, a part isn’t fully deburred until it has a radius on each edge.
DEBURRING & EDGE-ROUNDING - RADIUS
At this stage of the process, the primary and secondary burrs are removed and the edges rounded off. In order to lay the foundations for subsequent process steps (powder coating, wet painting, galvanisation, anodisation, bonding, etc.) and rule out any risk of injury due to sharp edges, the removal of the primary respectively secondary burr is often combined with the so-called edge-rounding. The edge rounding range from a few decimillimetres to radii of 2mm or even greater. These radii are now stipulated by standards such as e.g. DIN EN 1090.
The deburring and edge-rounding is carried out using flexible, abrasive tools with high adaptability to internal and external contours such as radii, boreholes and cut-outs. The corresponding deburring discs, deburring wheels, deburring blocks and deburring brushes are used on portable machines as well as grinding and deburring machines. The last mentioned machines have, for example, planetary head systems or oscillating units for uniform processing of the edges.
A good edge rounding result is characterized by removing the sharpness on the edges of your laser-cut or punched materials. This prevents injuries that may be caused by handling the material, while simultaneously improving downstream processing. Furthermore, a radius at the edge of the materials also improves paint adhesion.
Are you looking for the most beautiful and best rounding of metal?
A radius is created on the edge of the metal during edge rounding of metal products. This ensures that the sharpness of the edge is removed and it is given a uniform rounding. We offer perfection in edge rounding with a radius of up to two mm in a single pass.
OXIDE REMOVAL
If you are cutting via a CO2-laser or Fiber Laser with oxygen, we have the solution that removes any oxide layers along the cutting edge of the material. Oxygen-cut workpieces have oxide layers on the cut edges. These „dark layers“ pose a risk for subsequent processes and can lead for example to chipping of the coating. For that reason they must be removed.
Mechanical removal of the oxide layer is achieved by grinding or brushing. Both processing options can be implemented for manual processing procedures. In terms of mechanical processing, it is mostly brushes that are used, which, thanks to a specially developed wire fill in an innovative multi-row arrangement, flexibly follow the contours of the workpiece and achieve blank metallic edge surfaces.
Profimach offers a wide range of deburring machines that also can remove your laser oxide. Our OEM factory developed in the beginning of 2015 a new brush Barrel to remove the laser oxide skin from laser-cut steel. This brush is to be used in the models with standard Rotary brush barrel machines (PRO Steel Versatile-Series) combining the excellent edge rounding and deburring results of the machine with the required oxide skin removal both from the interior as well as exterior contours ot the product.
If you have rusty surfaces, we have the solution that removes any oxide layers along the surface of the material. Steel, iron, aluminium, copper, magnesium,...
FINISH-GRINDING
Punched, fine blanking, stamped and laser-cut parts often require high demands on the surface. A beautiful surface is a pleasant side effect of the deburring process. In some cases, a specific type of surface finish could be necessary.
The purpose of this process step is to grind out scratch marks and create a decorative surface. Specific grinding patterns right up to a high-gloss mirror finish can be achieved on the sheet metal surfaces.
During the last processing step, it is primarily abrasive cloth, nonwoven abrasive, and felting tools that are used, as a continuous belt or roller. With manual processing techniques, the results, and their reproducibility, depend heavily on the operator. For mechanical finishing, the machine must have appropriate setting options.
Grinding with the express goal of removing material and decreasing material variation. This process removes the exterior oxide layer/skin and grinds the material much like a surface grinder – only using a wide belt abrasive. We do reach surface flatness within 0.02mm on 1700 mm width.
Pro Steel® Series
Pro Steel® Series | Small Bur removal | Bur removal | Slag removal | Edge Rounding | Laser Oxide removal | Rust Removal | Surface finish | Calibrating |
---|---|---|---|---|---|---|---|---|
PRO Steel® M Series - Manual Grinding and deburring Machines | ||||||||
PSDM-Manual Serie | +++ | +++ | + | + | +++ | +++ | ++ | + |
PSTM-II Manual Serie | +++ | +++ | + | + | +++ | +++ | ++ | + |
PRO Steel® AD-Series - Automatic Deburring Machines | ||||||||
Automatic Deburring with Planetary abrasive Barrels Brush | ||||||||
PRO Steel® PSG-Versatile Series | +++ | +++ | + | + | +++(opt) | ++(opt) | - | - |
PRO Steel® PSGR-Versatile PLUS Series | +++ | ++++ | ++ | ++ | +++(opt) | ++(opt),- | - | - |
Automatic Deburring with Vertical rotating brush | ||||||||
PRO Steel® PSD Flexy Series | ||||||||
PRO Steel® PSG2D-Deslag Series | + | +++ | ++++ | + | - | - | - | - |
PRO Steel® PS3D-Deslag Heavy Duty Series | + | ++ | ++++ | + | - | - | - | - |
Automatic dual side Deburring machines | ||||||||
PRO Steel® PS2T2C-Two-Side Series | +++ | ++++ | ++ | +++ | + | + | - | - |
PRO Steel® AD-PSBK-Two-Side-PLUS Series | +++ | ++++ | +++ | +++ | + | + | - | - |
PRO Steel® AD-PSBKG-Two-Side-PRO Series | +++ | ++++ | +++ | +++ | ++ | ++ | + | - |
PRO Steel® ad-PSGB-Laser Series | ++++ | +++ | - | ++++ | - | - | - | - |
Automatic Surface finishing Machines | ||||||||
PRO Steel® PSR-Surface Series DRY | ++ | ++ | + | - | ++ | +++ | ++++ | + |
PRO Steel® PSR-W-Surface Series WET | ++ | ++ | + | - | ++ | +++ | ++++ | + |
PRO Steel® PSRD-Surface PLUS Series | +++ | +++ | ++ | + | +++ | +++ | ++++ | + |
PRO Steel® PSR2D-Surface PRO Series | ++ | +++ | ++ | + | +++ | +++ | ++++ | + |
PRO Steel Series : Code key = P-x-S-y-z-000-w
How to read the machine types?
Code | P-x-S-y-z-000-w | component unit |
---|---|---|
x | Digit between P-S | |
2 | Two sides simultaneously up and down deburring | |
y | First digit after PS (Profimach Sander) | |
- | Automatic operation | |
M | Manual operation | |
z | codes placed in sequence of machining | |
2-3-4-5-6 | Number BEFORE letter is the quantity of the letter following | |
B | Brush full width | |
C | Chain Belt transversal | |
D | Disk brush vertical | |
H | Disk Brush vertical with hammer function | |
G | Gyro or planetary barrel brush or fladder type | |
R | Roller- Contact roller with full width abrasive belt | |
T | Transversal Small Belt | |
OOO | Width of working surface in mm | |
w | at the end after width value | |
W | Wet working | |
II | Second Generation | |
III | Third Generation | |
- | Dry working |
Plane sheet metal deburring batch processing
Many flat sheet metal processing customers (eg, stamping, laser cutting, etc.) have no particularly demanding requirements for deburring accuracy, but need to meet large-scale deburring processing. The basic requirements of these customers must be two:
The first is that the plane and corners are all polished and deburred; the second is high efficiency. This can meet the needs of high-volume processing and reduce costs by improving efficiency. In response to this situation, a three-unit deburring machine, multi-function deburring and polishing chamfering equipment provided by Us has been recognized by customers.
The machine is composed of a set of sanding wheels + a set of brush + polishing wheel.
First of all, the work efficiency is high. The sanding wheel grinding process has the advantages of heavy cutting and deburring processing and high processing efficiency. Because the flat workpiece has a large deburring area, the workload is large and the edges are small. Only by first solving the ergonomic bottleneck of planar processing, the entire deburring process can be accelerated.
The second function is all. The sander is highly efficient, but it can only be machined on the plane, but the corner deburring is powerless. The brush disk configuration can only be processed on the edge but not on the plane. By combining the two processes, it is possible to complement each other, which not only satisfies the deburring requirements, but also enables efficient machining. In addition, the sander also has a drawing function, and the polishing wheel can make the surface treatment more perfect
Plane sheet metal deburring machine. Using the universal grinding wheel to rotate at high speed, the sand line slides over the corner surface of the workpiece, and the burrs are evenly removed and the chamfered corners are precisely processed. The main part is chamfered, and the friction on the plane is very small.
Description:
1. Low cost: consumables are unbound and limited
2. Fast processing speed, according to the processing efficiency requirements, optional single or multi-unit models, processing line speed adjustable from 0.1-35 meters per minute
3. Variable frequency adjustment to meet various processing needs
4. Uniform processing, while not hurting the positive plane, does not hurt the protective film
5. Easy to operate, put the product on the conveyor belt and send it automatically through the machine
6. Cutting friction force digital display, frequency, conveying speed digitally concise and stable
7. The finished product is not deformed after processing, high efficiency, does not affect dimensional accuracy and thickness.
Applications – individualised and modular
The requirements of industry and craftsmanship are extremely diverse.
Different punched or cut components and materials require increasingly specialised machining procedures.
We devote ourselves to the changing requirements for deburring, finishing, de-slagging, edge rounding and surface grinding of metals and provide suitable quality grinding technologies as an efficient and affordable solution.
As our customer, you will find with us the best quality solution for your requirements at the most affordable price.
New technology in the fabrication industry has given the metal fabricator more options to produce parts for their customers. Fiber laser cutting machines, in particular, allow the fabricator to cut more parts in a day than it ever could with CO2 lasers. Automated load and unload systems attached to these laser cutting machines also allow the shop to cut almost 24/7. Punching machines, Stamping lines, fine blanking lines gives even bigger output of parts to be deburred.
While fabricators can cut parts more quickly than ever before, they have to deal with other bottlenecks downstream from the laser or press. Depending on the cut quality or customer requirement, they might need to deburr, edge-round, or remove the oxide layer on a part. Adding more people to the deburring department has been the traditional way of attacking the deburring issue. However, increased labor costs, lack of efficiency, lack of consistency, and the need to provide a safer working environment have led companies to search for a different solution: automated deburring.
To stay competitive and get parts out of the shop in a timely fashion, fabricators should look at automating the deburring process just as they did with the laser cutting process. Investing in an automated deburring machine makes sense for a modern cleaner metal fabricating environment. Management realizes true labor savings. Shop floor morale picks up as people are freed from the hard and monotonous work of manually grinding edges. Older workers are less likely to hurt themselves doing this taxing work. Customers receive parts that are consistent and in the best shape to be painted or powder coated.
It’s hard to overlook all of the benefits when they are clearly presented.
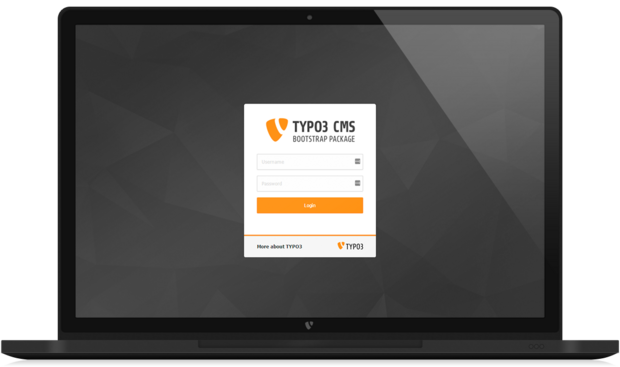
We are upgrading our website to serve you better
Profimach deburring machines, Jonsen Sander deburring machines, Jonsen sander, deburr and edge round punched/stamped and laser-cut parts, double-sided deburring, single side deburring, Oxide removal and surface finishing, deburring, deburring machine, deburring Machines, FLAT DEBURRING MACHINE, plate deburring machine, sheet deburring machine, deburring solution, automated deburring, edge rounding, edge processing, rounding, deburr and edge round, clean edge, oxide removal, surface finish, grinding, hand grinding, double-sided, single-sided, single pass, punched, laser, laser beads, cut, thin sheet metal, parts, burrs, splatters, light burrs, laser deburring, high quality results, small parts, brushes, quick change, three dimensional, industrial sheet metal processing, economical deburring, Metal Polishing Machines, deburring brush, metal parts with burrs, sheet metal with burrs, metal parts with burrs, punched parts with burrs, laser parts with burrs, plasma parts with burrs, flamecut parts with burrs, heavy burrs, light burrs,