WET or DRY?
Deburring machines come in wet and dry varieties. Dry machines may be less expensive, but they do require some kind of dust collector—either dry (basically a big vacuum cleaner) or wet (which forces all grinding debris into a wet tank to cool and capture the debris, reducing the risk of fire or explosion).
Dry machines work well for grinding certain parts of similar material—all carbon steel, for instance. But wet deburring machines are an absolute must when grinding different metals, such as aluminum, which can produce combustible dust. If combustible dust is left in a dry dust collection system when steel is run, the sparks created from the steel can ignite the remaining dust, causing a fire or explosion. A wet system, on the other hand, creates no metal dust and so usually does not present such hazards.
Wet machines typically have ancillary equipment, such as a filter and a drying unit. The filter separates the grinding debris from the coolant and recirculates the coolant to spray where the grinding is taking place. The drying unit can include squeegee rolls that push the coolant off of a deburred and grained part, as well as a blower that removes the remaining liquid.
In most applications, wet deburring machines can prolong the life of abrasive media. With the right coolant, abrasive media can last even longer. Using water-soluble coolants—usually 95 percent water mixed with 5 percent coolant chemical—may almost double abrasive life versus using water alone.
Neither wet nor dry machines are maintenance-free. For dry systems, technicians periodically must vacuum internal components to remove leftover metal fines. With a wet machine, an operator can use the hose attached to the coolant pump to wash internal components. On all systems, operators must grease bearings periodically. They also need to adjust certain elements, such as the tension on pinch rolls, which must hold the material properly against the conveyor belt.
Should you use a wet or dry deburring machine?
Each system has its advantages and disadvantages.
Wet deburring machines flood coolant into the work area. Gravity returns the coolant with dirt and grinding particles to a filter that catches the particles and recycles the coolant to the main tank. Some machines have a filtering system as a stand-alone unit, while others have a filtration unit under the machine to save space. Wet systems eliminate the need for a dust collector, offer long belt life, and minimize hazards when working with different metals.
Wet systems do require a strict maintenance regimen. Certain coolant mixtures work best with certain materials, and excessive corrosion occurs if proper water and lubricant mixtures are not maintained. A number of factors affect the water chemistry in a machine. For example, regular tap water has sodium, calcium, magnesium, and sulfur dissolved in it, and as water evaporates from the tank it leaves these harmful minerals behind.
Daily cleaning and monitoring the chemical makeup of the coolant are vital for optimal machine performance. Some wet machines have stainless steel in critical areas to prevent corrosion. A few machines are made entirely of stainless steel to suit even the most rigorous applications.
Bearing life is the most troublesome problem with wet machines. On some newer systems, pressurized bearings prevent moisture from entering, but this is a relatively new, somewhat untested technology. As always, proper maintenance is the most effective solution.
Dry machines can require less maintenance, provide a longer machine life, and can be less expensive to purchase and operate. However, it is very important to be aware of potential problems. Aluminum dust can accumulate in ducting, and all it takes is one spark to start a fire. Again, maintenance is critical, and cleaning the machine after changing from one material to another is essential.
Dry machines also can leave dust particles and grit on the part surface. If those flat parts are not cleaned, they can prematurely wear press brake tooling, which can be expensive, especially if you’re using hardened, precision-ground punches and dies.
Dry systems also require either dry or wet dust extractors. Dry extractors are adequate for collecting dust from various processes. They must be changed regularly and disposed of properly. However, they do pose some serious hazards if they aren’t maintained properly. Dry filters consist of cloth, paper, synthetic, and other materials. Various metals, abrasive grits, brush fibers, and oil residue can get into the filters, and a hot spark could cause a fire. Check with your fire department for local laws on dust collection.
This is why wet dust extractors have become some more popular. They eliminate the cost of regular filter changes and disposal. But more important, the filter medium—usually just tap water—saturates the particles and quenches any hot sparks. The dust is pulled into a water wash or scrubbing system, and particles settle to the bottom where they can be removed easily. Most wet filters are stainless steel, so rusting isn’t a problem.
Most heavy-duty grinding applications are done dry. When running both aluminum and steel in the same machine, a wet dust collector must be used to prevent fires caused by ignition of the dust. Regardless of what collector you use, though, it is imperative that you check and clean ductwork daily to eliminate any fire hazard.
Ultimately, the type of machine and options you choose will depend on the type of burr removal and finish you require. The decision between a wet or dry machine, and the options needed, should be made after samples have been run by the machine builder.
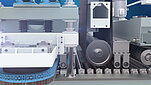
WET vs. DRY
A basic decision that must be considered is whether the material should be processed in a wet or a dry machine. Wet and dry machines both process the material in the same way; wet machines simply add coolant that is sprayed on the part as it is processed.
Dry Machines are often the first choice because they are generally less expensive to purchase and often have a longer life. However, there are numerous advantages to processing materials on a wet machine.
Wet Machines include a filter unit that also pumps the coolant on the part, and usually include a drying unit that removes the coolant from the part as it leaves the machine.
Several advantages of a Wet Machine are:
• A significant factor when choosing wet versus dry is the possibility of fires when a variety of metals will be processed on the same machine. Some metal dust (such as aluminum) is very flammable, and in a dry machine this dust can be ignited by the spark created when running steel. Timesavers recommends the use of a wet machine when a single machine will be used to process different metals.
• When processing dry, heat buildup due to friction of the abrasive belt on the work piece can cause unwanted warping, particularly on thin materials. A wet machine virtually eliminates this possibility.
• Wet processing improves abrasive belt life due to reduced friction, heat and loading that occurs when grinding dry.
• Wet processing usually provides a finer finish (a lower the RMA) when same grit belts are used to process wet versus dry.
• Parts processed on a wet machine exit clean and dry where-as a dry machine sometimes leaves residual dust on parts.
• A dry machine requires dust collection which means the dry system will have two foot-prints (one for the grinder, one for the dust collector), while a wet machine usually has one footprint.
• Should you choose to process dry, Timesavers recommends the use of a Wet Dust Collector attached to the dust hood/s of the sander. Wet dust collectors capture metal grinding dust in a reservoir that must be cleaned regularly.
• Wet machines do cost more and require more maintenance to achieve these advantages however in most cases the positives outweigh the negatives.